Course description
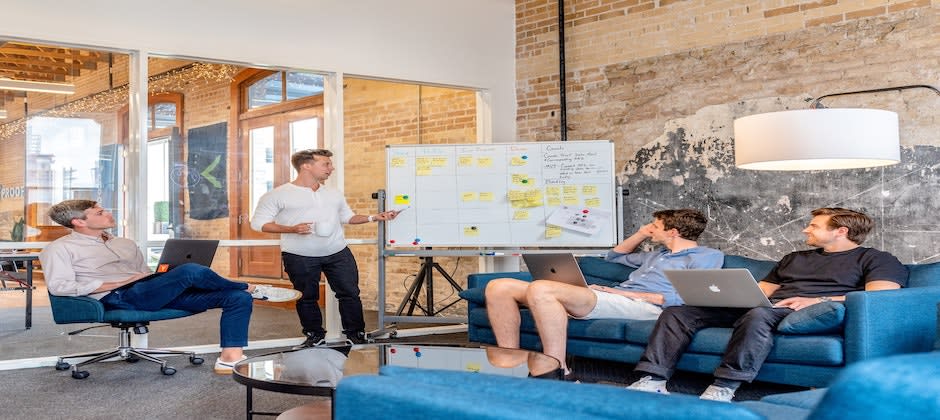
This practical 2-day course is designed to allow front line employees to both gain understanding about applying Lean and eliminating waste from the process.
The Yellow Belt course offers hands-on exercises, as well as interactive discussions to
reinforce the learning. Participants of the course will be able to conduct root cause analysis and apply tools to solve their business problems to improve EBITA (Profit Margin) and customer satisfaction.
Do you work at this company and want to update this page?
Is there out-of-date information about your company or courses published here? Fill out this form to get in touch with us.
Upcoming start dates
Who should attend?
- All Front employees who are involved in day to day tasks and processes in front/back office.
- Candidate has ability to identify a Business Challenge that is within their function to solve.
- Project duration is typically less than 30 days.
- A senior member (Company Sponsor) will interview candidates to assess: Aptitude / Willingness / Capability.
Training content
- Yellow Belt Course Outline:
A3 Methodology: Use Lean-based PDCA to solve problems. - Lean Tools: Apply Lean concepts to eliminate Process Waste and non value-added steps to focus on customer outcome.
- Root Cause Analysis: Apply Structured Problem Solving tools using Six Sigma to identify root cause.
- Kaizen Events: Learn how to conduct fast track workshops to solve problems.
Certification / Credits
Yellow Belt certification is achieved after successful completion of 1 project.
Contact this provider
University of North Texas - PDI | Innovative educations to prepare agile data-driven leaders
PDI has provided education, information and training for more than four decades. 500,000 professionals have gained the tools and knowledge that increase performance on topics ranging from oil and gas accounting to financial management, private investigations, legal and business skills....